All industrial companies are required to keep their cranes in good condition in order to facilitate safe and effective operations. Cranes need the same level of care for maintenance as cars need for oil changes in order to function properly. In this guide, we will detail crane maintenance procedures to safeguard your equipment’s efficiency through scheduled preventive inspections.
Why Crane Maintenance is Crucial for Operational Efficiency
Routine checks pick up on small problems before they turn into serious hazards. If operators don’t do regular maintenance, they leave themselves vulnerable to surprise failures that can delay whole projects and cost them huge repair bills.
Good maintenance habits increase productivity by having the crane available for use when required. Also, well-maintained cranes last longer, and this can cost companies thousands in replacement costs. The calculation is straightforward – a couple of hours spent on upkeep each month avoids weeks of expensive disruption.
The Key Components of Crane Maintenance
Every crane has critical parts that need special attention. The brakes maintain control over heavy loads, while wire ropes hold the heavy lifting. Electrical and Electronic systems drive the crane’s motions, while hoists perform the lifting tasks.
These parts face constant stress and wear down over time. Regular greasing keeps moving parts gliding smoothly, while inspections catch fraying wires or worn brake pads early. When operators take care of these key components, the whole crane works better and lasts longer.
Crane Maintenance Procedures: A Step-by-Step Guide
Crane maintenance follows a clear schedule. Daily checks include looking over wire ropes for damage, testing brakes, and checking limit switches. Operators should grease all moving parts, inspect hook latches, and test limit switches. Monthly maintenance gets even more thorough, with detailed inspections of electrical and electronic systems, and safety devices.
Following these steps helps catch problems early:
- Check all oil levels and look for leaks
- Inspect wire ropes for wear, kinks, or broken strands
- Test all brakes and limit switches
- Listen for unusual noises during operation
- Check structural components for surface cracks
- Ensure all safety devices work properly
- Document all findings and maintenance performed
Preventive Maintenance: The Best Way to Avoid Breakdown and Costly Repairs
Preventive maintenance spots trouble before it causes breakdowns. Regular inspections catch worn parts before they fail, while proper lubrication prevents excessive wear. This proactive approach keeps cranes running longer and safer. It also helps companies stay within safety regulations and avoid fines. When operators make prevention their priority, everyone benefits from safer, more reliable equipment.
How Routine Maintenance can ensure Annual Crane Inspection passes with ease
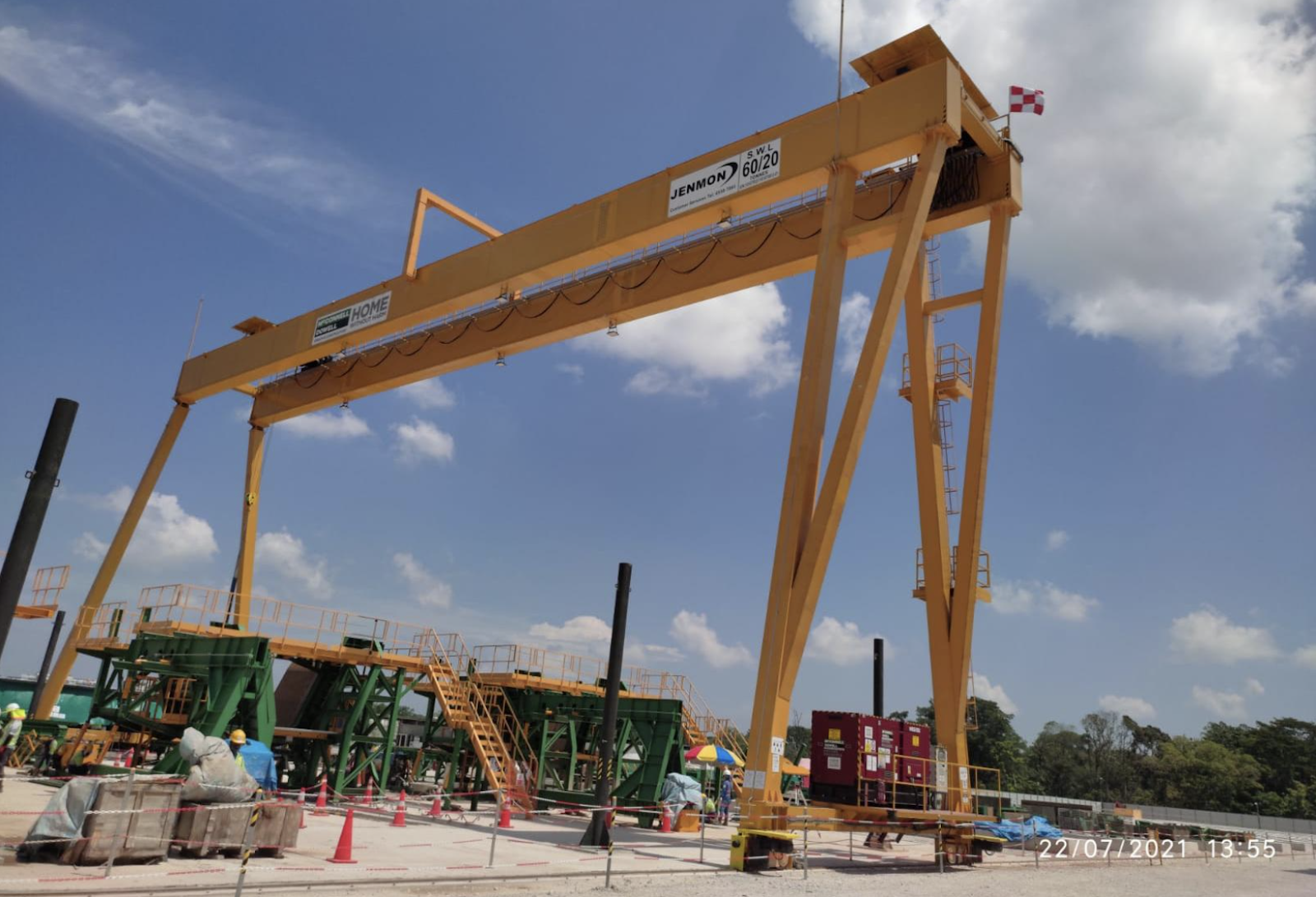
- Annual Inspection: Visual Inspection: Move around the crane, inspect for visible damage and search for loose bolts, broken welds, or harmed parts. Check wire ropes for signs of wear or damage
- Every 4 years Inspection: Load Testing: Perform basic load tests if required and check for unusual noises or movements. Verify brake operation under load as well.
Conclusion: Keep Your Crane Running Smoothly with Regular Maintenance
Regular maintenance makes a crane reliable instead of a costly nuisance. Spending time and resources on maintenance translates into fewer malfunctions, increased safety, and a longer life for equipment. Crane operators understand that preventing issues is always better than fixing them. Don’t let problems happen – take action today to get your crane performing at its best. Call Jenmon today for professional crane maintenance service that keeps your equipment lifting efficiently and safely.